Materiały filtracyjne wykorzystywane w filtracji plackowej
Materiały filtracyjne wykorzystywane w filtracji plackowej S. Ripperger
Filtracja plackowa jest rodzajem filtracji powierzchniowej, w której oddzielona substancja stała osadza się w formie placka filtracyjnego. Po pewnym czasie zachodzi konieczność jego usunięcia z materiału filtracyjnego. Czas odstępów pomiędzy kolejnymi etapami filtracji zależy między innymi od stężenia substancji stałej w zawiesinie, hydraulicznego oporu placka filtracyjnego, powierzchni filtra i możliwej do osiągnięcia różnicy ciśnień. W przypadku filtrów bębnowych lub tarczowych, pracujących w trybie ciągłym, czas trwania interwałów zależy od prędkości obrotowej bębna lub tarczy, a dla filtrów taśmowych – od ilości obrotów taśmy na jednostkę czasu. Gdy interwały filtracyjne są krótkie to okazuję się, iż dobór materiału filtracyjnego ma bardzo istotne znaczenie na przebieg całego procesu filtracyjnego. Okazuje się bowiem, że w takiej sytuacji wstępna faza filtracji, w której zwykle uzyskuje się duże przepływy objętościowe filtratu , określa całkowity przepływ filtratu. W poniższym przeglądzie podjęto próbę przybliżenia najistotniejszych informacji dotyczących dostępnych materiałów filtracyjnych stosowanym w filtracji plackowej.1. Wstęp W przypadku filtracji plackowej, oddzielona substancja stała osadza się na całkowitym polu przekroju materiału filtracyjnego. Dopóki placek filtracyjny nie zostanie do końca uformowany, materiał filtracyjny spełnia bardzo istotną rolę. W początkowej fazie filtracyjnej ma on decydujący wpływ na zatrzymanie cząstek, narastanie placka i przepływ objętościowy filtratu. W dalszym etapie filtracji ważniejszą rolę przy separacji cząstek zaczyna pełnić placek filtracyjny, natomiast materiał filtracyjny jest tylko jego nośnikiem. W tej części procesu wpływ placka filtracyjnego na przepływ filtratu jest dominujący. W fazie końcowej filtracji plackowej interakcja między materiałem filtracyjnym a plackiem filtracyjnym ma znaczenie przy wyładowywaniu placka.
2. Materiały filtracyjne
W przypadku filtracji plackowej znalazły zastosowanie najróżniejsze substancje porowate.
Materiał filtracyjny używany przy filtracji plackowej powinien się charakteryzować następującymi właściwościami:
- niskimi oporami przepływu,
- wystarczającą stabilnością mechaniczną,
- chemiczną i termiczną odpornością w określonych warunkach operacyjnych,
- wystarczającym zatrzymaniem cząstek, szczególnie w początkowej fazie filtracji,
- minimalnym stopniem zabrudzenia,
- małą częstotliwością serwisowania,
- właściwościami powierzchniowymi promującymi oderwaniem się placka i czyszczenia,
- w przypadku drobnych porów, właściwościami powierzchniowymi pozwalającymi na łatwe nawilżenie,
- niską ceną,
- w przypadku zastosowania w przemyśle spożywczym i farmaceutycznym bezpieczeństwem toksykologicznym.
Oczekiwania stawiane procesowi separacji na tkaninie filtracyjnej znacznie różnią się między sobą, dlatego bardzo ważnym problemem staje się proces optymalizacji procesu. Należy rozważyć wymagania procesowe i własności materiałów filtracyjnych i starać się znaleźć między nimi pewną równowagę. Rysunek (po prawej) przedstawia najważniejsze czynniki, które muszą być przeanalizowane dla procesu filtracji plackowej.
2.1. Tkaniny
Tkaniny są stosowane przy rozdzielaniu cząstek o rozmiarach powyżej 1 μm. Tkaniny produkowane są przy wykorzystaniu różnych kombinacji splotów krzyżowych między nićmi wątku a nićmi osnowy. Najprostszą metodą splotu jest metoda splotu koszykowego, w której nić wątku jest prowadzona przemiennie w poprzek i poniżej nici osnowy. W standardowym splocie skośnym, nić wątku jest prowadzona ponad i poniżej dwiema nićmi osnowy. Skutkuje to równoległym przebiegiem, a nawet wyrównaniem między nićmi wątku w kierunku nici osnowy. Inne typy splotu, np. splot satynowy, zostały stworzone poprzez przesunięcia punktów połączeń, które pozwalają stworzyć wzór powtarzający się w określonych interwałach.
Wyróżnia się przędze z włókna pojedynczego i przędze wielowłókienkowe, jak również przędze z włókien odcinkowych. Przędza włókna pojedynczego składa się z dużej ilości włókien, które są splecione, przeplecione lub skręcone. Średnice włókien są głównie okrągłe, ale mogą mieć również inne kształty. Spotykane są również struktury ziarniste i warstwowe. W takim przypadku przędza jest owinięta dodatkowymi włóknami. Kiedy tkanina jest wytwarzana z pojedynczego włókna, to poza porami tkaniny, które są zależne od typu splotu, zauważalne są przestrzenie porowate w niciach pomiędzy pojedynczymi włóknami. Struktura porów szarej tkaniny, a przez to również własności procesu filtracji jest definiowana przez rodzaje nici wątku i osnowy (pojedyncze włókno), odpowiednią delikatność włókna, grubość nici wątku i osnowy i rodzaju splotu. Tkaniny różnią się między sobą, głównie w zakresie własności dotyczących przepływu, separacji, usuwania placka i oczyszczania. Istnieją tak zwane metody udoskonalające do dalszej poprawy własności filtracyjnych tkanin. Struktura może być skurczona lub utrwalona za pomocą działania termicznego. Opalarka wypala i usuwa wystające pory. Kolejną często stosowaną metodą jest kontrolowanie, gdzie tkaninę prowadzą podgrzewane rolki. Nicie są spłaszczane pod wpływem ciśnienia i wysokiej temperatury, przędze z pojedynczych włókien są sprasowywane, pory tkaniny są zwężane i wyrównywane, a powierzchnia jest wygładzana. Podobnie jak własności absorpcyjne i zwilżające, własności elektrostatyczne włókna mogą być bezpośrednio zależne od różnych chemicznych i fizycznych zmian powierzchni. Może być to osiągnięte poprzez modyfikację lub powlekanie struktury z użyciem chemikaliów. Wszystkie te czynniki mogą wpływać na procesy separacji cząstek i usuwania placka.
Dostępne zróżnicowane opcje produkcji i modyfikacji tkanin pozwalają na niemalże perfekcyjną adaptację do odpowiednich wymagań. Tkaniny z przędzy z pojedynczych włókien mają względnie gładką powierzchnię, która pozwala na łatwiejsze formowanie placka niż w przypadku zastosowania tkanin z przędzy wielowłókienkowej. Zarówno tkaniny wielowłókienkowe, jak i wielowarstwowe promują filtrację wgłębną, i w ten sposób również pojawiające się ryzyko zabrudzenia.
Tkaniny wielowarstwowe są projektowane i dobierane w taki sposób, że najniższa warstwa (po stronie przepływu) pełni funkcję decyzyjną w kwestii transmisji energii (np. w filtrze taśmowym) oraz efektach odprowadzania cieczy podczas wypływu filtratu, podczas gdy pierwsza warstwa zasadniczo decyduje o przebiegu filtracji. Materiały są dostępne w postaci metalicznej (półki sitowe) oraz jako włókna sztuczne bądź naturalne. Włókna tekstylne budowane są zwykle z substancji syntetycznych, np. polipropylenu (PP), poliestru (PES), poliamidu (PA), poliakrylonitrylu (PAN), polieteroeteroketonu (PEEK), polifluorku winyldienu lub politetrafluoroetylenu (PTFE).
2.2. Inne materiały filtracyjne
Włókniny produkowane są poprzez sklejanie lub sczepianie włókien tekstylnych. Są one zwykle wysoce porowate. Do klejenia włókien można stosować lepiszcze, lub też włókna mogą być osadzone bezpośrednio po wirowaniu w konsystencji ciastowatej, tak, że łączą się one między sobą w miejscach kontaktu (tzw. tkaniny spunbonded). Przeplatanie realizuje się np. za pomocą igieł, które perforują powierzchnię z wysoką częstotliwością. W związku z występowaniem tarcia takie działanie scala włókninę. Podobny efekt może być również uzyskany przy wykorzystaniu silnych strumieni wody. Włókniny są produkowane w bardzo rozmaitych rodzajach ze względu na strukturę i ułożenie warstw (patrz /6/). Koszty produkcji są względnie niskie. Bardziej wytrzymałe włókniny mogą być uzyskane przez osadzenie dodatkowych nici lub tkanin (włókniny wzmocnione). Włókniny mogą być również retrospektywnie ulepszone. Zasadność stosowania filcu igłowego dla potrzeb filtracji plackowej została potwierdzona testami i uzyskana w trakcie badań /7, 8/. Membrany do mikrofiltracji rozdzielają cząstki o rozmiarach z zakresu 0.05 do 5 μm. W połączeniu z mechanicznym odwilżaniem placków filtracyjnych, ich stosowanie jest również polecane w procesach filtracji plackowej (zob. sekcja 7.). Membrany są dostępne w postaci różnych polimerów, materiałów ceramicznych, węgla i metali.
3. Charakterystyczne własności materiału filtracyjnego dla filtracji plackowej
W celu scharakteryzowania materiału filtracyjnego określane są różne parametry. Tkaniny są charakteryzowane głównie przez cechy mierzalne, czyli gramaturę (g/m2), grubość tkaniny, przenikalność powietrza przy określonych różnicach ciśnień, największą siłę rozciągającą i odkształcenie, oraz objętość porów /2-4/. Aby dane medium mogło zostać zastosowane jako materiał filtrujący, dodatkowo ustalone są parametry związane z filtracją, takie jak opór materiału, ciśnienie punktu wrzenia dla określenia maksymalnego rozmiaru porów oraz krzywej separacji cząstek. Wykonywane są również zdjęcia, które następnie poddaje się analizie i przeprowadza testy sprawdzające.
3.1. Przenikalność czynnika ciekłego
Zależność strat ciśnienia od szybkości przepływu może być wyrażona następującym równaniem:

We wzorze tym ρ to gęstość cieczy, η- lepkość dynamiczna. Stałe K1 i Kt zależą od struktury tkaniny i wyznaczane są doświadczalnie. Pierwsze wyrażenie uwzględnia przepływ laminarny, podczas gdy drugie staje się znaczące zakresie przepływu turbulentnego. W większości przypadków wytwórcy określają opór materiału filtracyjnego poprzez ustalenie przenikalności powietrza (przepustowość powietrza przy różnicy ciśnień 200 Pa). Przełożenie tych wartości na praktyczny przypadek filtracji cieczy jest możliwe technicznie tylko z odpowiednią dokładnością, jeśli zastosowana zostanie zasada podobieństwa i liczba Reynoldsa jako parametr odniesienia (użyta we wzorze na liczbę Reynoldsa średnica to w tym szczególnym przypadku średnica włókna). W przypadku włókien cienkich, dużej lepkości i małej prędkości, drugie wyrażenie może być często zaniedbane, co oznacza, że można korzystać z korelacji Darcy’ego. W takim przypadku, Kt oznacza przenikalność i jest ona jednocześnie odwrotnością wartości oporu.
Efekty zależne od czasu mogą pojawić się w wypadku napęcznienia włókien. W takich rzadkich przypadkach struktura ulega zmianie w czasie pierwszego przepłukiwania a powtarzalne mierzone wartości mogą być po raz pierwszy określone dopiero po fazie tzw. formowania. Podczas wykonywania pomiarów można zaobserwować, że tylko różnica ciśnień jest określana przez materiał filtracyjny. Całkowite nawilżenie struktury porów jest również obserwowane w przypadku, gdy mamy do czynienia z materiałem hydrofobowym (zob. sekcja 3.2). Modele opisujące przepłukiwanie tkanin z przędzy wielowłókienkowej zostały przedyskutowane w /9/.
3.2. Powierzchnia i zachowanie zwilżające
Dla odpowiednio cienkich porów, właściwości powierzchni zewnętrznej i wewnętrznej mogą wpływać na zachowanie się materiału filtracyjnego podczas obciążania go cieczą. Materiał filtracyjny z powierzchnią hydrofobową oraz wąskimi porami jest początkowo poddawany perfuzji powyżej ciśnienia nawilżenia. W innych przypadkach, do początkowego przepłukiwania całkowicie nawilżonej tkaniny przez ciecz powyżej ciśnienia nasycenia może służyć powietrze. Nawilżanie powierzchni ciała stałego zwiększa powierzchnię kontaktującej się nim cieczy. Zastosowanie wolnej energii międzyfazowej σ (napięcia powierzchniowego) wyrównuje tę różnicę. W stanie równowagi, powierzchnie międzyfazowe znajdują się w stanie ustalonym i wraz z powierzchnią ciała stałego tworzą kąt zwilżania. Jest to parametr ilościowo opisujący zwilżalność powierzchni ciała stałego. Wyróżnia się pojęcia: zachowania zwilżającego i niezwilżającego. Wiele polimerów ma niską zwilżalność wobec wody. Dodatkowa modyfikacja powierzchni może w bardzo dużym stopniu zmienić jej własności zwilżające. Jedynym rezultatem niskiego stopnia zwilżalności może być fakt, że niektóre wgłębienia w materiale filtracyjnym nie mogą być przepłukiwane przez ciecz. Może się tak stać w np. w przypadku tkanin z przędzy wielowłókienkowej, jeśli woda przepływa pomiędzy przeplecionymi nićmi, ale nie może penetrować struktury porów samych nici. Tak zwana bariera kapilarna pojawia się przy kątach zwilżania z zakresu Θ>90° (ciśnienie penetracji). W takim wypadku, napięcie powierzchniowe cieczy w połączeniu z niewielkim rozmiarami porów prowadzi do sytuacji, w której penetracja układu porów w materiale filtracyjnym jest możliwa dopiero wtedy, gdy osiągnięta zostaje bariera ciśnienia. Dla porów cylindrycznych o średnicy dP, sprowadza się to do zależności:
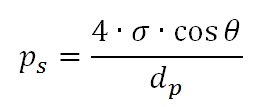

Dla Θ>90° cosinus ma wartość ujemną, zatem ujemna wartość wyrażenia wskazuje na istnienie bariery ciśnienia. Równanie jest również prawidłowe dla Θ<90°. W takim wypadku, w związku z włoskowatością układu, system porów w tkaninie jest całkowicie wypełniony cieczą. Siły powierzchniowe działają tu w ten sposób, że pory otwierają się na poddawanie perfuzji gazem dopiero przy różnicy ciśnień powyżej ciśnienia nasycenia. Według korelacji, największe pory są poddawane perfuzji gazem przy powolnym wzroście ciśnienia. W przypadku struktury włókienniczej, która jest całkowicie zanurzona w cieczy, rozpoczęcie perfuzji jest równoznaczne z tworzeniem się bąbelków gazu. Dlatego też, odpowiadające tej sytuacji ciśnienie to również ciśnienie nasycenia. Poprzez pomiar ciśnienia nasycenia możliwe jest określenie średnicy największego pora w badanej powierzchni, przy znanych wartościach σ i Θ. Należy mieć na uwadze, że jest to średnica równoważna pora o takiej samej powierzchni. Zazwyczaj w celu określenia ciśnienia nasycenia stosowane są rozpuszczalniki organiczne, które zwilżają większość materiałów samorzutnie.
3.3. Zatrzymanie cząstek
W przypadku filtracji plackowej, zatrzymanie cząstek na materiale filtracyjnym jest związane głównie z następującymi mechanizmami:
- zjawiskiem bariery,
- uzyskiwaniem stabilnej pozycji,
- formowaniem mostków,
- adhezją do powierzchni wewnętrznej.
Zjawisko bariery
Efekt przesiewania jest najbardziej trywialnym przypadkiem zjawiska bariery. Jeśli cząstka jest większa niż rozmiar porów, zostaje odseparowana. Jeśli wszystkie cząstki ciała stałego, znajdujące się w zawiesinie, mają rozmiary większe niż największe pory materiału filtracyjnego, zatrzymanych zostanie 100% tych cząstek. W przypadku filtracji plackowej nie zawsze udaje się kontynuować tego typu działanie, ponieważ przepływ filtratu jest ograniczony przez odpowiednio wysoki opór materiału filtracyjnego. Dla porównania, jest to również zjawisko pojawiające się w przypadku tak zwanej filtracji sterylnej lub filtracji absolutnej, generującej ciecze sterylne lub ultra czyste. Podczas, gdy cząstki perfundują materiał w związku z ekspansją przestrzenną, niektóre z nich są również prowadzone w stronę powierzchni wewnętrznej materiału filtracyjnego i mogą być oddzielone w związku z występowaniem sił adhezyjnych. Proces ten nazywa się intercepcją.
Uzyskiwanie pozycji stabilnej
Cząstka zostaje odseparowana również wtedy, gdy następuje jej kontakt z kilkoma włóknami tkaniny w tym samym czasie i przybiera ona pozycję stabilną. Szczególnie w przypadku włóknin można zaobserwować, że dodatkowe cząstki akumulują się w takim miejscu i tworzą skupiska. Cząstka osiąga pozycję stabilną, jeśli dochodzi do jej kontaktu ze strukturą włókna lub uprzednio odseparowaną cząstką przynajmniej w trzech punktach.
Formacja skupisk we włókninie
Blokowanie porów (tworzenie mostków)
Zawieszone cząstki o rozmiarach znacznie mniejszych niż rozmiary porów materiału filtracyjnego są odseparowywane w związku z blokowaniem porów. W pewnych warunkach, cząstki hamują się nawzajem w taki sposób, że podczas przechodzenia przez por mogą się akumulować w jego wnętrzu i tworzyć mostki. Wtedy może rozpocząć się formowanie placka filtracyjnego. Aż do czasu rozpoczęcia formacji takiego mostka, cząstki mogą swobodnie przechodzić przez pory, co na tym etapie skutkuje tworzeniem się mętnego filtratu.
Zjawisko zapychania się porów pojawia się w większości procesów wykorzystujących filtrację plackową, ponieważ rozmiary porów wybranych materiałów filtracyjnych są prawie zawsze większe od rozmiarów cząstek w zawiesinie. Istnieją pewne przybliżenia empiryczne, pozwalające na prognozowanie zjawiska zapychania porów /10, 11/. Według nich stężenie cząstek, stosunek rozmiarów cząstek do rozmiarów porów, szybkość przepływu, oraz w konsekwencji również różnica ciśnień, rozkład rozmiarów cząstek i wzajemne oddziaływanie między cząstkami zawiesiny a materiałem filtracyjnym to parametry, które pozwalają określić, czy dojdzie do zapchania porów, czy też nie. Akumulacja cząstek jest bardziej prawdopodobna jeśli pojawiają się oddziaływania elektrostatyczne o charakterze przyciągającym miedzy materiałem filtracyjnym a cząstkami.
Adhezja do powierzchni wewnętrznej
W procesie filtracji plackowej mechanizm adhezji jest szczególnie istotny przy tworzeniu mostków i skupisk. Siły Van der Waalsa oraz oddziaływania elektrostatyczne to czynniki, które mają w tym wypadku podstawowe znaczenie. W przypadku urządzeń, w których stosuje się tkaniny oraz znając zawartość i rodzaje jonów w roztworze (a w związku z tym również wartość pH), możliwe są znaczące zmiany w oddziaływaniach elektrostatycznych między cząstkami w tkaninie. Oczyszczanie tkaniny jest również w sposób zdecydowany zależne od warunków adhezyjności.
4. Testy filtracyjne
Chronologiczny proces filtracji plackowej jest zależny od własności produktu, który ma być poddany procesowi (np. lepkość cieczy, jej skład, rozmiary i struktury cząstek ciała stałego) oraz od powierzchni filtra. W większości przypadków, powierzchnię dobiera się w taki sposób, by przy dużym stężeniu substancji stałej placek filtracyjny zaczął się formować jak najszybciej. Testy filtracyjne, prowadzące do zaprojektowania filtra, odbywają się przy użyciu konkretnej zawiesiny i konkretnego materiału filtracyjnego, używanych później w układzie o skali przemysłowej. Stosuje się tutaj głównie małe filtry testowe. Tryb pracy filtra testowego może się różnić od trybu pracy filtra używanego w konkretnych zastosowaniach. W testach laboratoryjnych określenie własności filtracyjnych prawdziwej zawiesiny ma znaczenie pierwszorzędne. W skład badań pilotujących wchodzi również sprawdzenie pracy małego filtra w dość długim okresie czasu pracy. Testy dostarczają informacji na temat separacji, formowania placka filtracyjnego, oczekiwanego oporu placka oraz właściwego przepływu filtratu, który zależy od wcześniej wymienionych parametrów. W ramach testów możliwe jest również zbadanie możliwości przemywania placka i jego mechanicznego osuszania. VDI wytyczna 2762 opisuje metodę pomiaru oraz odpowiednią aparaturę pomiarową do określania oporu placka filtracyjnego /12/. Anlauf /13, 14/ dostarcza informacji na temat poprawnego przeprowadzenia testów, oszacowywania ich rezultatów oraz możliwych do wystąpienia błędów. Tichy /15, 16/ przedstawia zaawansowaną technologię pomiarową. Autor udowodnił, że w przypadku wystąpienia krótkich interwałów, zarówno objętość filtratu, jak i straty ciśnienia w czasie muszą być mierzone bardzo dokładnie, a znaczące błędy mogą pojawić się podczas użycia standardowych urządzeń przy określaniu efektywnego oporu materiału filtracyjnego. W celu dobrania optymalnej tkaniny filtracyjnej sugeruje się wykonanie testów w kilku cyklach filtracyjnych. Okazało się, że zachowanie materiału filtracyjnego w późniejszym okresie funkcjonowania może być rzetelnie oszacowane po przeprowadzeniu od 20 do 30 cykli /8, 17, 18/. Weigert również badał mętnienie filtratu oraz adhezję placka w tym procesie /19/. Wyniki jego badań pokazują, że regularny proces cykliczny w odniesieniu do zjawiska mętnienia filtratu podczas formowania placka filtracyjnego na tkaninie oraz właściwego przepływu filtratu może być uzyskany dopiero po 10 do 30 cyklach. Po tym okresie pojawia się niemalże równomierne „zanieczyszczenie” placka filtracyjnego. W celu objaśnienia występowania wyżej wspomnianego zjawiska poniżej przytoczone zostaną rezultaty przykładowego testu. Podczas testu zastosowano tkaninę w oryginalnej formie (tkanina: nieprzetworzona, etykieta: nieprzetworzona) oraz w formie przemysłowo sklasyfikowanej (etykieta: Ind). Stanowisko testowe zostało opisane w /17/.
Rysunek (po prawej) pokazuje przepływ filtratu w pierwszym, dziesiątym i pięćdziesiątym cyklu, przy zastosowaniu tkaniny sklasyfikowanej. Wskazuje również różnice w zachowaniu podczas pierwszego cyklu pomiędzy tkaniną nieprzetworzoną a sklasyfikowaną. Podczas przeprowadzonych testów ciśnienie filtracyjne w układzie wytwarza się w czasie ok. 15 sekund. Następnie, rozpoczyna się filtracja pod niemalże stałym ciśnieniem.
W związku z budową placka filtracyjnego, przepływ filtratu spada zdecydowanie w pierwszych cyklach. Redukcja natężenia przepływu filtratu po kilku cyklach jest oczywista, ponieważ następuje zapchanie tkaniny. Rysunek (po prawej) przedstawia zmiany zmętnienia filtratu. Jasno widać na nim, że zmętnienie, wywołane przez cząstki na tkaninie jest niewielkie na początku cyklu filtracyjnego.
5. Efektywny opór materiału filtracyjnego
Jeśli jako RM0 wskazuje się opór materiału filtracyjnego, przez który przepływa czysta ciecz, możliwe jest również wzięcie pod uwagę dodatkowego oporu RMS, spowodowanego zanieczyszczeniem materiału. Dodatkowo, liczne testy (np. /16, 20/) pokazują, że opór materiału filtracyjnego RM jest wyższy już podczas pierwszego cyklu filtracyjnego, co oznacza, że dla nowego materiału filtracyjnego ta wartość ma większe znaczenie niż RM0. Dzieje się tak, ponieważ na powierzchni przejściowej między materiałem filtracyjnym a plackiem występuje dodatkowy opór, nazywany oporem interferencyjnym RMI. Tichy /16/ opisał ten dodatkowy wpływ ilościowo za pomocą współczynnika K1, definiowanego jako:
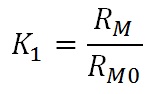
Tichy przeprowadził 93 testy filtracyjne z użyciem różnych tkanin i zawiesin. Określił głównie wartości K1 z zakresu 14 do 40, ale pokazał również, że możliwe jest pojawienie się wartości nawet powyżej 100. W literaturze można znaleźć doniesienia na temat „zapychania się porów” (np. /21, 22/). Jednakże, jak dotąd przeprowadzono bardzo niewiele testów dotyczących zahamowania przepływu na powierzchni przejściowej między plackiem a materiałem filtracyjnym. Grace /22/ umieścił w równaniu filtracji „wielkość zapchania” w celu uwzględnienia dodatkowych oporów związanych z osadzaniem się cząstek na materiale filtracyjnym. Tichy /16/ użył prostego modelu otworu sferycznego do ilościowego opisu najważniejszych oddziaływań mających związek z parametrami geometrycznymi. Jego rozważania pokazują, że przy niekorzystnym doborze materiału filtracyjnego i połączeniu różnych rodzajów cząstek, rozmiaru przestrzeni między kanałami oraz kształtów kanałów i ich rozmiarów, może pojawić się bardzo duży opór dodatkowy. W najprostszym przypadku (idealnie okrągłe kanały i monodyspersyjne, koliste cząstki mniejsze niż przestrzenie między kanałami i większe niż ich średnica), cząstki mogą spowodować zatkanie wszystkich porów, czego rezultatem będzie nieskończony dodatkowy opór. Model tłumaczy korzyści wynikające ze stosowania porów prostokątnych, które są powszechne w sitach szczelinowych i tkaninach. Rozważania uwzględniające rozkład rozmiarów cząstek wyjaśniają, że ułamek cząstek, które mają rozmiar równy rozmiarowi porów, ma bardzo istotne znaczenie. To właśnie głównie ta grupa cząstek powoduje wystąpienie dodatkowego oporu podczas osadzania się na porach. Rozważania pokazują również, że opór interferencyjny może mieć mniejszy wpływ w zawiesinach z aglomeratami. Rezultaty uzyskane przez Anlaufa /20/ również dowodzą, że efektywny opór materiału filtracyjnego w przypadku tkanin może różnić się nawet dziesięciokrotnie, w zależności od rodzaju i stanu zawiesiny.Rezultaty pokazują, że należy rozpatrywać efektywny opór RM, który pojawia się w filtracji plackowej. Składa się on z:
- oporu materiału filtracyjnego w stosunku do przepłukiwania czystą cieczą RM0
- dodatkowego oporu zanieczyszczeń szczątkowych RMS
- oporu interferencyjnego RMI.
Zatem możemy zapisać

Doświadczenie pokazuje, że mądry dobór materiału filtracyjnego może zminimalizować opór związany z zanieczyszczeniami resztkowymi oraz opór interferencyjny. Możliwe ulepszenia zostały również zaprezentowane w /23/.
6. Wpływ efektywnego oporu tkaniny filtracyjnej na proces filtracji plackowej
W początkowej fazie filtracji efektywny opór materiału filtracyjnego to parametr decydujący dla przepływu filtratu. W przypadku krótkiego cyklu filtracyjnego, całkowita ilość zużytego filtratu jest zasadniczo określana w fazie początkowej. Teoretycznie, korzystnie jest przeprowadzeni procesu metodą filtracji krokowej z krótkimi interwałami filtracyjnymi oraz krótkim przestojami na usunięcie placka i wyczyszczenie materiału filtracyjnego (odtąd oznaczonymi jako czas usunięcia tR). Pozwala to na użycie często dużych objętości filtratu w początkowej fazie filtracji. Z drugiej strony, czasy usuwania tR i czas filtracji tF powinny pozostawać w stosunku optymalnym. /23/ objaśnia korelację dla filtracji krokowej przy stałej różnicy ciśnień. Punktem wyjścia jest tutaj równanie filtracji plackowej przy stałej różnicy ciśnień (zob. /24/). Właściwą objętość filtratu zużywaną w czasie filtracji tF (objętość filtratu na powierzchnię filtra) można przedstawić jako:
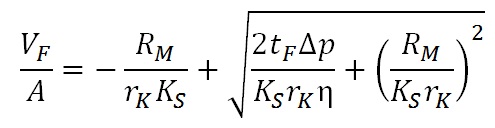
Po zakończeniu filtracji, placek filtracyjny musi zostać oderwany i usunięty. Czas potrzebny na usunięcie placka i wyczyszczenie materiału filtracyjnego to zakłócenie filtracji. Dlatego też, średnia objętość właściwa zużyta podczas interwału filtracyjnego (filtracja plus czyszczenie) wyraża się jako:
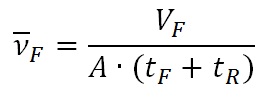
Poniżej, za pomocą prostych obliczeń, wyjaśniony zostaje wpływ materiału filtracyjnego na wartość średniego przepływu objętościowego filtratu. Zakładamy, że stężenie substancji stałej w strumieniu zasilającym wynosi ok. 0.025 % obj., co odpowiada wartości czynnika KS równej 0.04. Dla materiału filtracyjnego zakładamy opór RM0 = 5*108 m-1. Właściwy opór placka filtracyjnego wynosi rK = 2*1012 m-2. Korzystając ze znajomości powyższych wartości, średnie właściwe natężenie objętościowe przepływu w zależności od czasu filtracji zostało obliczone dla oporu tkaniny filtracyjnej RM = RM0 =5*108 m-1 (zaznaczone na wykresie kolorem czerwonym) oraz dla RM = 40RM0 (niebieski). Rezultaty zostały przedstawione na ilustracji 9. Czerwona i niebieska krzywa różnią się, jeśli chodzi o wartość czasu usuwania tR. W przypadku czerwonej krzywej czas usuwania wynosi 5 minut, natomiast dla niebieskiej krzywej – 0.5 minuty. Oczywistym jest, że maksimum pojawi się dla dużego oporu efektywnego, czasu usuwania równego 5 minut, czasu filtracji ok. 8 minut oraz średniego natężenia przepływu filtratu ok. 5 m3/(m2h). Dlatego też, teoretycznie optymalnym rozwiązaniem jest usuwanie placka po tym czasie. Oczywisty staje się również fakt, że optimum nie jest tak silne, zatem dla dłuższego czasu filtracji, np. dla 20 minut, może wciąż być spełnione. Jeśli możliwa jest poprawa wartości oporu początkowego, który pojawia się podczas filtracji, poprzez dobór optymalnego materiału filtracyjnego, można uzyskać przybliżenie do krzywej koloru czerwonego, obliczonej dla oporu RM0. Optymalny czas filtracji przesuwa się wtedy do obszaru nieco niższych wartości.
Opisane powyżej tendencje są możliwe do zastosowania również wtedy, gdy czas usuwania redukuje się do 0.5 minuty. Uzyskanie krótkich czasów usuwania jest wykonalne jeśli stosowane są filtry automatyczne ciśnieniowe (automatic pressure filters). Jak zostało to zaprezentowane na wykresie, średnie właściwe natężenie objętościowe przepływu filtratu może być znacznie zwiększone przy zastosowaniu krótszego czasu usuwania tR. Wspomniane maksimum występuje również w przypadku krótkich czasów usuwania tR i krótkich czasów filtracji tF.
Dodatkowo, ostrożny dobór materiału filtracyjnego, czyli o niskiej wartości oporu efektywnego, może jeszcze bardziej zwiększyć średni przepływ filtratu. W takim wypadku optimum przesuwa się w stronę jeszcze krótszych czasów filtracji tF. Przykład pokazuje, że dobór materiału filtracyjnego jest bardzo istotny w przypadku krótkich interwałów filtracyjnych, ponieważ umożliwia znaczny wzrost wydajności.
7. Wpływ materiału filtracyjnego na osuszanie placka
Po zakończeniu filtracji, placek filtracyjny jest często osuszany mechanicznie poprzez wyładowywanie za pomocą sprężonego gazu. Dyspersja cieczy w systemie porów jest generalnie związana z kurczeniem się placka filtracyjnego. Kurczenie to ma związek z wewnętrznymi naprężeniami, spowodowanymi aktywnymi siłami kapilarnymi. Jeśli z powodu kurczenia w placku nastąpi przekroczenie maksymalnych przenoszonych naprężeń, poskutkuje to powstaniem pęknięć. Drugim z problemów jest osuszanie przy wstąpieniu różnicy ciśnień gazu, ponieważ natężenie przepływu gazu może wzrosnąć nawet stukrotnie. Konsumpcja gazu gwałtownie wzrasta, ciśnienie w strukturze porów spada, w związku z czym duże obszary placka filtracyjnego są pominięte przy osuszaniu mechanicznym. Wiedemann /25/ stwierdził, że proces tworzenia się pęknięć może być zredukowany poprzez zmniejszenie napięcia powierzchniowego. „Dociążenie” parą wodną pozwala zredukować napięcie powierzchniowe i w rezultacie ,możliwe jest uzyskanie niższych wartości sił kapilarnych. Dlatego też, często stosuje się tę właśnie metodę w celu zapobiegania pęknięciom /26, 27/. Można wyobrazić sobie, że wstępne prasowanie (wstępna konsolidacja) placka filtracyjnego ma wpływ na kurczenie i tworzenie się pęknięć. Testy dotyczące tego zagadnienia zostały przeprowadzone przez Wiedemanna i Stahla /26/. W przypadku prasowania wstępnego przy zastosowania wysokiego ciśnienia, placek filtracyjny zostaje ubity do takiego stopnia, że w przypadku dodatkowego usuwania cieczy nie zmienia on już swojego kształtu (zerowa kurczliwość).
W przeszłości podjęto wiele prób, mających rozwiązać problem występowania pęknięć przy stosowaniu metod mechanicznych, z użyciem specjalnych materiałów filtracyjnych. W przypadku tak zwanej tkaniny matrix (ang. matrix cloth), powierzchnia filtra jest podzielona na wiele małych, przepuszczalnych i nieprzepuszczalnych elementów. Ideą takiego rozwiązania jest to, że kurczenie i związane z nim siły mogą być tolerowane wzdłuż tak niewielkich powierzchni bez wystąpienia pęknięć. Rezultatem zastosowania tego typu struktury jest istnienie wielu małych sekcji w placku filtracyjnym, które nie wykazują żadnych pęknięć, w rozmiarze zależnym od danego produktu. Jednakże, aktywna powierzchnia filtracyjna zostaje zredukowana przez występowanie sekcji nieprzepuszczalnych.
Podczas używania mikroporowatego materiału filtracyjnego przy ciśnieniu penetracji kapilar (ciśnienie nasycenia) wyższym niż stosowana różnica ciśnień, gaz nie może perfundować przez materiał filtracyjny nawet mimo obecności szczelin. Za pomocą równania 2 możliwe jest wyliczenie, że ciśnienia penetracji kapilar dla wody w temperaturze 20°C, przy rozmiarach porów 5µm oraz kąta zwilżania 60° wynosi 2.8 bar. Wartości liczbowe pokazują, że należy zastosować materiał filtracyjny o bardzo małych rozmiarach porów. Wysoko porowate i cienkie materiały filtracyjne są konieczne, by móc uzyskać duże wartości przepływu filtratu. Odpowiednie materiały mogą być produkowane jako tkaniny o strukturze warstwowej lub jako ceramiczne tarcze o strukturze asymetrycznej. Testy w skali laboratoryjnej zostały przeprowadzone zarówno na membranach, jak i na filtrach bębnowych, tarczowych oraz taśmowych /28, 30/. Poza przepustowością gazu, wyniki testów membran polimerowych i filtrów tkaninowych nie wykazują wielkich różnic. Jednakże, ważnym jest, by pamiętać o konieczności stosowania membran o wysokim stopniu przepuszczalności. Aby uzyskać odpowiednią stabilność, specjalnie zaprojektowane w tym celu tarcze ceramiczne mają grubość kilku milimetrów. W porównaniu do cienkiej membrany polimerowej, mają one dużo większy opór perfuzyjny /31, 33/. Mimo to, dzięki swoim zaletom na polu osuszania przy wykorzystaniu różnicy ciśnień, są one wciąż stosowane w praktyce. Jak dotąd nie udało się wyprodukować połączenia membrany polimerowej z tkaninowym materiałem filtracyjnym o wystarczająco wysokim stopniu trwałości.
Literatura:
/1/ D.B. Purchas: Handbook of Filter Media. Elsevier Science Ltd., 1996\ /2/ J. Heymann, P. Böttcher: Textile Filtermedien-Beschaffenheit und Eingeschaften. Filtrieren und Separieren 11 (1997) 43-51 /3/ S. Ripperger, Ch. Schnitzer: Barrierwirkung von Geweben – Teil 1: Textiltechnische Charakterisierung und Barrieremechanismen. Filtrieren und Separieren 19 (2005) 3, 110-117 /4/ Ch. Schnitzer, S. Ripperger: Barrierewirkung von Geweben – Teil 2: Experimentelle Methoden von Gewebeeigenschaften. Filtrieren und Separieren 19 (2005) 4, 166-173 /5/ S. Ripperger: Barrierewirkung von Geweben – Teil 3: Auswahl von Geweben zur Kuchenfiltration. Filtrieren und Separieren 19 (2005) 6, 284-289 /6/ W. Albrecht, H. Fuchs, W. Kittelmann: Vilestoffe – Rohstoffe, Herstellung, Anwendung, Prüfung, Wiley-VCH-Verlag, Wienheim (2000) /7/ H. Xiaomin, L. Chunbo, D. Qifu: The use of polypropylene fibre needlefelt in the filtration of mineral slurries. Filtration and Separation 32 (1995) 4, 307-311 /8/ T. Wiegert, S. Ripperger: Das Verhalten von Geweben und Vilesen bei der Kuchenfiltration. Filtrieren und Separieren 11 (1997), 11-15 /9/ Ch. Shnitzer, S. Ripperger: Barrierewirkung von Geweben – Teil 4: Modellierung der Durchströmung von Multifilamentgeweben. Filtrieren und Separieren 21 (2007) 4, 226-231 /10/ A. Rushton, I. Hasaan: The effect of media structure on pore bridging and blocking. In: R. Weiler, R. de Bruyne (Hrsg.): Recent developments in filter media and their applications. Antwerpen (1980) /11/ A. Rushton, A.S.Ward, R.G.Holdich: Solid-liquid filtration and separation technology, VCH, Weinheim (2000) /12/ VDI-Richtlinie 2762: Filterbarkeit von Suspensionen – Bestimmung des Filterkuchenwiderstandes, Verein Deutscher Ingenieure, 1997. /13/ H. Anlauf: Standardfiltertests zur Bestimmung des Kuchen- und Filtermittelwiderstandes bei der Feststoffabtrennung aus Suspensionen (Teil 1). Filtrieren und Separieren 8 (1994) 2, 63 /14/ H. Anlauf: Standardfiltertests zur Bestimmung des Kuchen- und Filtermittelwiderstandes bei der Feststoffabtrennung aus Suspensionen (Teil 2). Filtrieren und Separieren 8 (1994) 3, 116 /15/ J. W. Tichy, S. Ripperger, U. Esser: Einfluss des Filtermittels auf den spezifischen Durchsatz von kontinuierlich betriebenen Filtern. Filtrieren und Separieren 19 (2005) 4, 162-165 /16/ J. W. Tichy: Zum Einfluss des Filtermittels und der auftretenden Interferenzen zwischen Filterkuchen und Filtermittel bei der Kuchenfiltration. Disseration TU Kaiserlautern (2007), erschienen als VDI-Forschritt-Bericht Nr. 877, Reihe 3, VDI-Verlag, Düsseldorf (2007) /17/ T. Weigert, S. Ripperger: Versuchsstand zur Untersuchung von Filtermitteln für die Kuchenfiltration. Chem-Ing-Techn. 68 (1996), 1473-1476 /18/ T. Weigert, S. Ripperger: Effect of Filter Fabric Binding on Cake Filtration. Filtration & Separation 34 (1997), 507-510 /19/ T. Weigert: Haftung von Filterkuchen bei der Fest/Flüssig-Filtration. Didderation TU Dresden (2000), erschienen als VDI-Fortschritt-Bericht Nr. 680, Reihe 3, VDi-Verlag, Düsseldorf (2001) /20/ H. Anlauf: Filtermedien zur Kuchenfiltration – Schnittstelle zwischen Suspension und Appart. Chem.-Ing.-Tech. 79 (2007) 11, 1821-1831 /21/ P.M.Heertjes: Chem. Eng. Sci. 7 (1958) 15 /22/ H. P. Grace: A. I. Ch. E. J. 2 (1956) 316 /23/ S. Ripperger: Barrierewirkung von Geweben – Teil 6: Einfluss des Filtermittels auf die Kuchenfiltration. Filtrieren und Separieren 22 (2007) 1, /24/ S. Ripperger: Filtration von Flüssigkeiten. In: Handbuch der Mechanischen Verfahrenstechnik, von H. Schubert (Hrsg.) Wiley-VCH (2003) /25/ Th. Wiedemann: Das Schrumpfungs- und Rissbildungsverhalten von Filterkuchen. Dissertation Universität Karlsruhe 1996. /26/ Th. Wiedemann, W. Stahl: Schrupfungs- und Rissbildungsverhalten feinkörniger Filterkuchen bei der Glassdifferenzdruckentfeuchtung. Chem-Ing.-Techn. 67 (1995), 1486-1489. /27/ St. Gerl: Damp-Druckfiltration – Eine kombinierte mechanisch/thermische Differenzdruckentfeuchtung von Filterkuchen. VDI Fortschrittbericht, Reihe 3, Nr. 604, VDI Verlag 1999. /28/ H. Anlauf: Kombination von Eindicker und kontinuierlichem Druckfilter zur Verbesserung von Fest/Flüssig- Trennprozessen. Chem.-Ing.-Techn. 61 (1989) 11, 686-693. /29/ R. G. Jung, R. Lotzien: Einsatz von mikroporösen Filtermitteln bei der Druckfiltration unterschiedlich beschaffener Rohstoffe. Aufbereit. – Tech. 30 (1989) 11, 193-196 /30/ H. Anlauf: Vakuum- und Druckfilter ohne Gasverbrauch. Filtrieren und Separieren 4 (1990) 3, 135-145. /31/ B. Ekberg, S. Wojtkowitz: Kuchenbildende Nassfiltration ohne Gasdurchsatz mit neuen keramischen Ecosue-Scheibenfiltern. Aufbereit. – Tech. 29 (1988), 193-196 /32/ S. Wojtkowitz: Keramik füllt eine Filtervakuum – Zur Theorie und Praxis der kuchenbildenden Filtration ohne Gasdurchsatz. Aufbereit. – Tech. 29 (1988), 594-602 /33/ S. Wojtkowitz, B. Ekberg: Kuchenbildende Nassfiltration ohne Gasdurchsatz. Filtrieren und Separieren 2 (1988) 1, 23-25. Prof. Dr.-Ing. Siegfried Ripperger TU Keiserlautern Post box 3049 D-67653 Kaiserlautern Phone +49 (0) 631 2052121 www.uni-kl.de/MTV
test

Firma ChemTech jest wysoce specjalistyczną firmą zajmującą się technikami separacji, filtracji procesowej, filtracji cieczy i gazów oraz oczyszczania i rozdziału faz.